Reinventing Wheels
Where did the American auto industry go wrong, and can UW-Madison help it get back on the road?
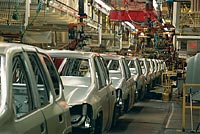
As American automakers work to get assembly lines up and running again, UW-Madison is taking the next steps — exploring alternative technologies, training engineers, and advising how companies must adapt to stay afloat. Photo: Getty Images
For a year, Detroit’s automakers have been sideswiped by downsizings, layoffs, and sell-offs.
The bumps in the road started more than a year ago, when $4-plus gallons of gasoline made consumers thirst for the high-mileage cars that United States firms have long loathed. In December 2008, thousands of union jobs disappeared as the last Chevy Tahoe rolled off the assembly line in Janesville, Wisconsin. In April 2009, Chrysler entered bankruptcy. And at the beginning of June 2009, General Motors — GM! once the lion of American business! — followed suit.
The blue smoke from the industry’s tailpipe threatens to sweep over UW-Madison, whose relationship with the auto industry dates to the days when American Motors manufactured cars in Racine and Kenosha. Just ten years ago, Detroit was a prized destination for UW engineering graduates, and even now, hundreds of engineering students participate in various car clubs and competitions. UW-Madison researchers are hard at work on developing better hybrid-drive systems. With an eye to reducing pollution and energy consumption, they are exploring exactly how fuel burns inside an engine, and investigating radical ideas such as mixing gasoline and diesel fuel to reduce pollution in diesel engines.
Yet the dead-serious game of bumper cars in Detroit lurches on.
Looking Under the Hood
The first component of an effective repair job is an accurate diagnosis: what went wrong in Detroit?
Former chancellor John D. Wiley MA’65, PhD’68, who once served as associate dean for research in the College of Engineering, thinks the industry ignored its customers for too long.
“They made really stupid decisions,” says Wiley, a former employee at Bell Laboratories, where the transistor was invented, who today serves as interim director of the public arm of the Wisconsin Institutes for Discovery. “The auto industry told us they were giving us what we want — big, heavy, high-powered cars loaded with features.” In reality, he says, the industry was creating demand through a sophisticated marketing campaign.
The ominous clanking had been heard in Detroit’s engine compartment for years before its joy ride came to a shuddering halt last summer, when a $20 bill could not even buy a stingy five gallons of gas. But, Wiley says, Detroit is a serial offender in self-delusion. “They also said they were giving consumers what they wanted in the 1950s, when VW came out with the Beetle and ate their lunch. They were singing the same tune in the 1970s, when Toyota and Honda put out cars that people really wanted, and they were scratching their heads, wondering why their business was going down. In the 1990s, people wanted inexpensive, economical, practical vehicles — and they came out with the SUV. This is insanity,” he says.
Rather than blaming American auto executives who run the companies, Bob Lorenz ’69, MS’70, PhD’84, a UW professor of electrical and computer engineering who also holds an MBA, points a finger at the owners. “We, the equity holders, have given the companies extreme pressure for immediate returns, for higher stock valuations. One of the best ways to do this, on a short-term basis, is to sell off the future — to not invest in the future. If you eliminate engineering expenses, you improve the bottom line in the short term,” says Lorenz. When executives respond to the short-term incentives in this way, he says, “the result is bad behavior.”
Research is expensive, and the great American industrial-research labs, pioneered by inventor Thomas Edison and adopted by flagship companies such as RCA and Kodak, have been declining since the 1960s.
But even as the auto industry and related manufacturers have cut back their in-house research efforts, they continue to see the wisdom of supporting research at UW-Madison.
Lorenz is co-director of the Wisconsin Electric Machine and Power Electronics Consortium, which for twenty-nine years has investigated devices that convert kinetic energy to electricity and vice versa — a core technology, for example, in hybrid vehicles and wind turbines.
During braking, these devices store the vehicle’s energy in the battery, and during acceleration, they reverse their role and recycle that same energy to supply driving force to the wheels. In conventional vehicles, brakes provide stopping power by converting the energy of motion into heat. But, Lorenz says, “it does not make sense to convert a lot of energy into heat.”
These power electronics are the key to hybrids, and hybrids are central to Detroit’s hopes, he adds. Despite success with the hybrid Prius, Lorenz thinks the technology is even better suited to heavy stop-and-go vehicles, such as delivery trucks and city buses. The consortium’s seventy international sponsors include Ford, GM, Toyota, Nissan, and Honda. “We have competitors supporting us because our long-term, pre-competitive explorations will produce technologies that industry will need in a decade,” he says.
A second industrial and governmental collaboration, the university’s Engine Research Center (ERC), occupies two floors of the Engineering Research Building, with an additional two laboratories in the newly remodeled Mechanical Engineering Building. In the basement of Engineering Research, eighteen heavily instrumented test cells resemble a hybrid of their own — auto shop, chemistry class, and computer lab. In some of the cells, engines are running under the watchful eye of an engineering student. In others, the engine and test equipment are in various stages of disassembly.
The center focuses on cleanly, efficiently converting the energy stored in hydrocarbon fuels, such as gasoline and diesel, into kinetic energy, says director David Foster ’73, MS’75, a UW-Madison professor of mechanical engineering. “One thing that makes this area of study so incredibly fascinating is that the energy carriers we use, liquid hydrocarbon fuels, are one of our most precious resources. In terms of energy density, they are far superior to anything else, typically over one hundred times as energy-dense as a good battery. The ability to carry a lot of energy onboard — to give a lot of range and high power — is unique to hydrocarbon fuels.”
The Secret Life of Cylinders
Although the price of oil has fallen from its peak last summer, most analysts think it will climb again as the economy recovers, and the Obama Administration has thrown down the gauntlet to auto manufacturers in the form of higher mileage standards. The key to meeting these standards, without raising tailpipe pollution, is hidden inside the cylinders of an internal-combustion engine, which inhale, compress, burn, and exhale a fuel-air combination several thousand times every minute.
The cylinder is an energetic, fast-changing realm, and dozens of parameters can be varied to affect pollution, performance, and efficiency. Metal engine walls are opaque, but in several engines at the ERC, researchers can shoot high-speed photos and perform laser diagnostics of an engine as it runs.
“Trying to understand and control the thermodynamics and combustion chemistry inside an engine is a huge challenge,” says Foster. “We get into the fundamental aspects of everything that occurs in the cylinder — how to introduce the fuel, how the fuel spray breaks up, the chemical kinetics of the combustion and emission formation processes, and fluid mechanics and heat transfer within the cylinder. As we continue to peel the onion, we get a better understanding of the technology of internal-combustion engines.”
One productive way to peel that onion is through computer simulation, and the ERC’s Rolf Reitz and Christopher Rutland, both UW professors of mechanical engineering, have spent years developing software that runs so-called “silicon engines.” Because these computational models require serious computer horsepower, the ERC has networked more than two hundred computers where, Reitz says, “we and our students can run advanced fluid-dynamics simulations of the whole process.”
These computers can support a process of continual improvement, he adds, and one computer study “can spend months exploring thousands of different combustion-chamber shapes and fuel-injection strategies. These are things you would never be able to do experimentally.”
Much of the work at the ERC concerns diesel fuel, which, although popular in European autos, is largely restricted to trucks and heavy equipment in the United States. Although diesel is inherently 30 percent more efficient than gasoline, it is also more prone to releasing soot and nitrogen oxide, a precursor of smog.
Hit the Road Running
Even as the American auto industry gets a thorough tune-up, about two hundred UW-Madison students are engaged in various engine-related activities. One team re-engineered a hybrid-drive system for a 2009 Saturn Vue, to improve fuel economy and reduce emissions, without detracting from performance, safety, or buyer appeal, and entered it in the federally sponsored EcoCAR Challenge. A second team is building an all-terrain vehicle with a ten-horsepower engine, while a third is refining an all-electric snowmobile for use by researchers in Greenland and Alaska, where delicate environmental measurements would be confounded by engine exhaust.
All of these efforts take advantage of student fascination with self-propelled vehicles to provide hands-on training that any potential employer can appreciate.
“We are trying to supply the industry with engineers who have a good background working with auto projects,” says Glenn Bower MS’89, PhD’92, an associate scientist at the ERC who guides these student groups. Because these competitions emulate the real world, “we can supply the companies with plug-and-play engineers; they don’t have to train them for two years. These engineers have the skills ahead of time that allow them to become productive very quickly.”
Sustaining Sustainability
If deficiencies in engineering are just part of the American auto industry’s dilemma, can UW-Madison help to improve management decision-making?
The skyrocketing price of gasoline, followed by the cliff-diving drop in auto sales triggered by the global recession, suggests that the industry has ignored the challenge of long-term survival, says Dan Anderson MBA’67, PhD’70, a professor of actuarial science, risk management, and insurance at the Wisconsin School of Business. He maintains that Detroit’s focus on gas-guzzlers and hostility to improving gas mileage represented a failure to grasp that businesses, like societies, must learn to stay afloat, even as the operating environment changes.
“I think the U.S. auto industry totally ignored an important sustainability condition — namely, that there is a finite amount of oil on earth,” says Anderson. “They never dealt with the question of what would happen if the price of gas went up substantially: Would people buy their cars, or should they be producing a more diverse lineup with the high-mileage cars that their customers would want?”
Anderson and others at the business school are teaching students to evaluate these questions during relatively new courses about environmental and social sustainability — training that can groom graduates for recently created positions as “chief sustainability officer” at many large corporations. Although cynics may dismiss the trend as window dressing, Standard & Poor’s has established a sustainability index to rank companies’ ability to thrive years into the future.
Anderson says the index is one indication that the concept of sustainability may itself be sustainable.
Had the American automakers acceded to tighter fuel-efficiency standards, they might be selling high-mileage cars to buyers who fear a renewed rise in gas prices, Anderson continues, noting, “The government was ahead of them, and they were stuck in their old ways.” Unlike Toyota, whose Prius has been a success story, “[Detroit] did not have any kind of strategy for what would happen if the price of gas went up, and people quit buying their heavy cars,” he says. “And when that happened, they got clobbered.”
Becoming Nimble
As the economy shut down last fall, automakers were saddled with a staggering load of unsold inventory, partly because of the momentum built into its production process. Traditionally, many auto suppliers start making parts several weeks before they are needed on the assembly line, says Franklin Rath ’73, MS’84, a program director for engineering professional development. When a sudden recession or a soaring fuel price — or both — crushes demand, he says, “your pipeline is full of parts and materials for cars, and you are going to keep making cars until you can shut off the pipeline.”
In the 1990s, the Center for Quick Response Manufacturing, where Rath was then associate director, helped tractor-maker John Deere overcome a similar problem at its plant in Horicon, Wisconsin. In a wet spring, the company was burdened with tractors they couldn’t sell. In a good spring, the company ran short of tractors, yet slow delivery of parts prevented it from making replacements quickly enough to sell before summer weather shut down demand. Deere, with input from Rath and his colleagues at UW-Madison, began working with suppliers, helping them to produce parts in two weeks. This build-to-demand strategy helped the company eliminate millions of dollars of inventory and offers a lesson for auto companies, Rath says.
Yet, faster is not always better in the auto business, as Lorenz learned from studying Toyota’s introduction of the Prius. “This was a classic case of doing it right, of leading the market without threatening to sink the company,” he says. Instead of trying to sell 100,000 Priuses the first year, the company produced only 10,000 cars annually for three years, giving it time to make sure customers were happy. Had a fatal flaw been exposed in the car’s radical hybrid technology, “Toyota could have bought them all back if necessary,” says Lorenz.
Although the strategy decreased the short-term profit, Toyota made it work, and last year Prius sales helped it displace GM as the largest auto manufacturer in the world.
Calling All Engineers
A simple change in tempo will probably not be enough to save Detroit, and the College of Engineering’s Bower says students are keenly aware of the upheaval in the heart of the American industry.
“Even the students working on the hybrid project have talked to me, worrying that even if they can get a job, they will be laid off,” he says. “There is a lot of concern from new engineers about what industry they should work in. I don’t think the auto industry is going away, but it is going to change dramatically.”
Reassuringly, the engineering skills used to build cars can be adapted to manufacture vehicles for agriculture, construction, and the military. And ironically, the tighter pollution and fuel-economy standards that are pinching the auto industry represent good news for engineers.
“In the end, we are getting away from one-fix-all technology,” says Bower, adding that the advent of all-electric cars and the rise of hybrids are only part of a rapid transportation transformation. “We will not settle on one solution to mobility,” he says. “The shell of the automobile will look the same, but in the end, we will need more power-transfer engineering. The engines will become more and more sophisticated, with more sensors and more electronic controls.
“In the end, we’ll need more engineering, not less.”
David Tenenbaum MA’86 is a Madison freelance writer and feature writer for The Why Files, an online magazine that explores the science behind the news at whyfiles.org.
Published in the Fall 2009 issue
Comments
No comments posted yet.